Forging Plans Together
Heinz-Peter Reichel has been working on different projects with the Hereon’s Magnesium Innovation Centre MagIC since 2005. During this time, various magnesium-based forgeable alloys have arisen for applications in the aerospace and automotive industries as well as in medical technology. Reichel met with Dr Norbert Hort, head of Hereon’s “Magnesium Processing Department”, for a project meeting in the centre’s Magnesium Casting Hall.
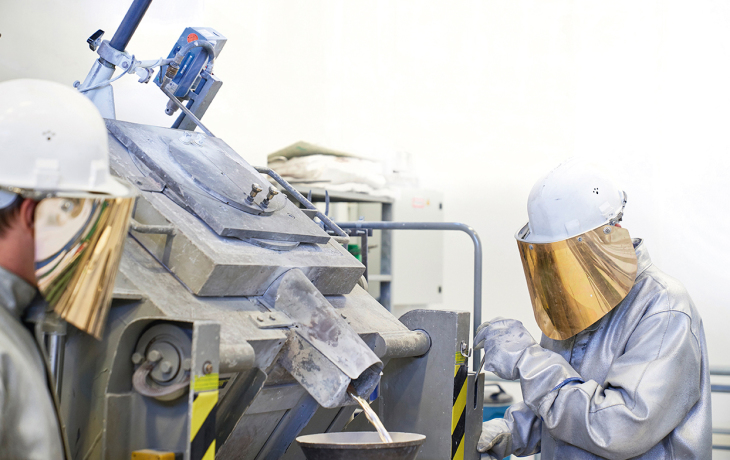
Photo: Hereon/Christian Schmid
Mr Reichel, do you still remember the fi rst project with the Hereon?
Heinz-Peter Reichel: It started in 2005 with a forged magnesium component, which had to have a petrol and benzene resistant surface. It should be used, for example, for a car petrol tank neck or for the fuel filler flap. The alloy wasn’t defined any further, so the scientists from Geesthacht developed a new alloy for us.
What became of it?
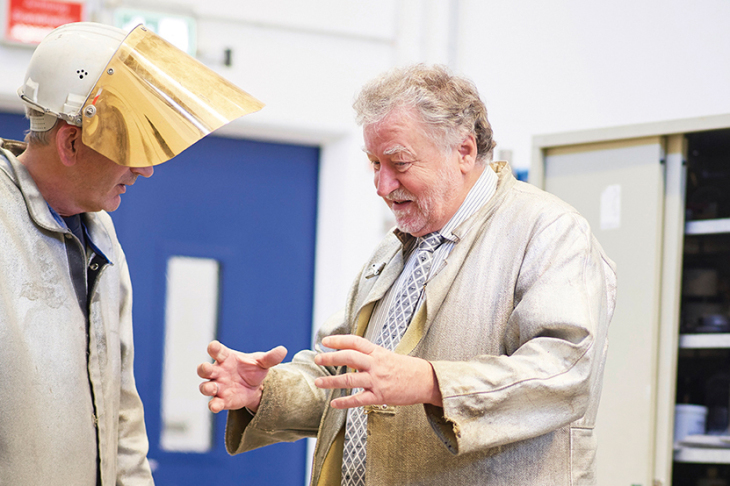
Heinz-Peter Reichel has been working with his colleagues at MagIC for nearly twenty years. Photo: Hereon/Christian Schmid
Heinz-Peter Reichel: We collaborated on the MagBone project from 2007 to 2009, in which magnesium implants were developed. The magnesium alloy had to be biodegradable and a bone screw was the target application. At the time we were dealing with blood interactions with the material. The alloy was invented and patented by Dr Norbert Hort. We took over the forging.
Mr Hort, can you tell us more about the MgBone project?
Norbert Hort: Implants made of a mixture of hydroxylapatite and magnesium were to be produced in the project. Molten magnesium, however, reacts with hydroxylapatite and can produce toxic phosphine. Magnesium casting therefore was not an option. So we ground the magnesium alloy together with the hydroxylapatite, a bonelike material, in a ball mill. The alloy then needed to be compacted so that it produced a compact metal body. This massive body could be processed further by the LMpv firm. In the end, a biodegradable bone substitute was created.
How does a typical collaboration between the two of you look?
Heinz-Peter Reichel: For certain applications, we often need a new alloy for forging. This must initially be developed, and that is where the scientists come into play. The Hereon then, for example, carries out a large part of the microstructure characterization, be it with the electron microscope or at the Hereon synchrotron facilities. The alloy development and production is thus undertaken by Norbert Hort and his team. Our company, LMpv, casts a five-centimetrethin plate, then the Weisensee cuts this plate into suitable pieces - for example, by forging. Finally, a component such as the seat structure for aircraft seats is produced. This is normally the end of the project - that is, when such a demonstrator has been created.
What is special about the alloy for the seating structure?
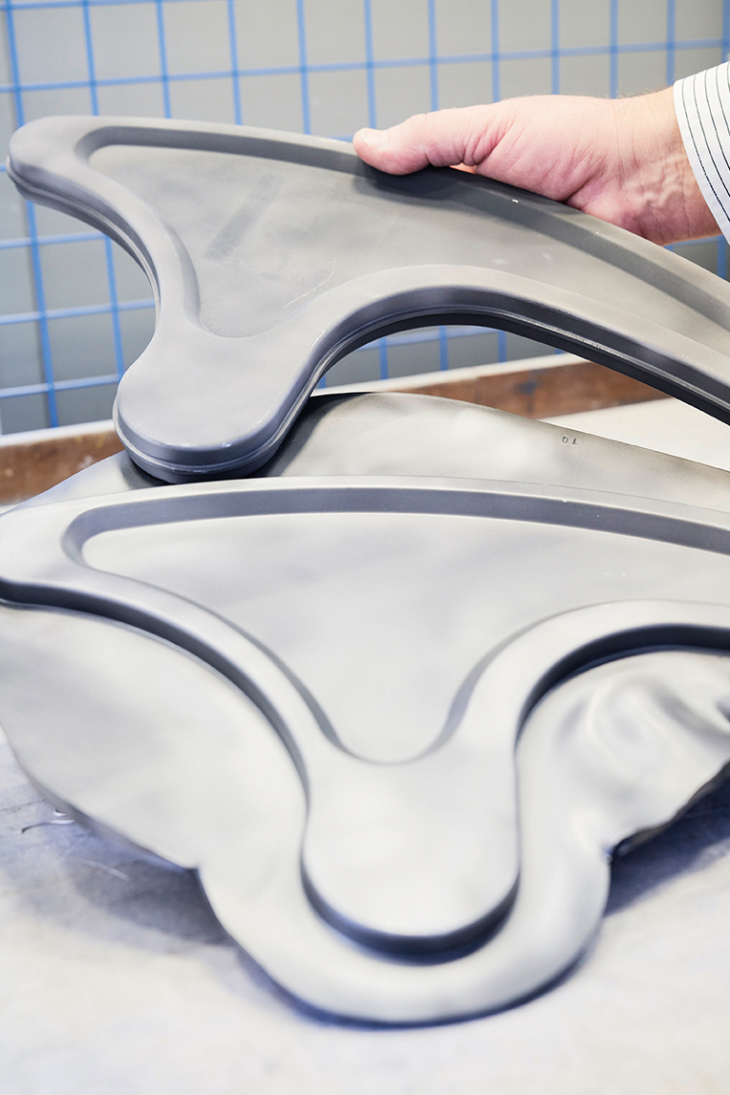
Part of an aircraft seat made from a magnesium alloy. This prototype came about through a collaborative project. Photo: Hereon/Christian Schmid
Heinz-Peter Reichel: The component and/or the alloy is noticeably less prone to burning than conventional components. This alloy burns only at higher temperatures than one thousand degrees Celsius - that is, around three hundred degrees higher than aluminium. Our alloy, however, has the disadvantage that it can’t be forged very well. It’s a lovely material for casting, but not for forging. Unfortunately, cast structures have completely different properties than those that are forged. Expressed another way: the cast seat would collapse much faster than the forged seat because the latter can better bear the load. In a follow-up project, we therefore want to deal with elongating the metal. To do so, we use additives such as silicon in the alloy, which are finely ground to about fifty nanometres. But we encountered tremendous difficulties in coaxing this silicon dust into dissolving and sinking into the molten mass. This is comparable to milk powder in coffee; it sometimes just floats on top. And when you use a spoon to stir it, half of it sticks to the spoon. We still have a great deal of work ahead of us.
Norbert Hort: We do, however, have a very good idea of how it might go. We have ideas as to how we could stir in the particles on a laboratory scale. But it’s only with larger quantities that we can see if and how this alloy is forgeable and what properties it will then have. This is where LMpv enters the picture, as a partner in larger scale applications. The LMpv material is then again studied using our scientific methods.
Thank you for the interview.
The interview was conducted by Heidrun Hillen (Hereon).
Published in the in2science #8 (June 2019)